Predictive Maintenance in Smart Factory – Aggity
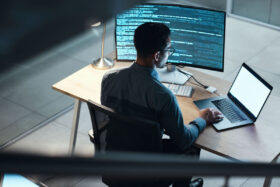
Predictive maintenance is an advanced technique used in Industry 4.0 and, specifically, in the Smart Factory, which uses data, sensors and analysis in order to predict errors and failures that may occur in machinery and industrial equipment so that the factory can anticipate their solution.
Tabla de contenidos
ToggleDiscover how predictive maintenance increases efficiency and reduces costs in the Smart Factory.
aggity is one of the most experienced companies in the Smart Factory environment. It specializes in the modernization of traditional factories, guiding them towards Industry 4.0 with innovative solutions, such as Smart Factory by aggity that, thanks to their use of the Internet of Things (IoT)Big Data or Artificial Intelligence, provides a complete, modern, configurable and modular system to manage and control the activities of production, quality, materials and, of course, the smart factory maintenance. This maximizes productivity and provides optimal industrial asset management.
These types of solutions are essential in industrial environments to improve their operational efficiency and also to increase the useful life of the equipment, which translates into reduced maintenance costs. In addition, implementing predictive maintenance in a production plant has other advantages such as reducing downtime and improving production and energy efficiency. But how does predictive maintenance work in the Smart Factory and what benefits does it provide?
Data collection
In order for a predictive maintenance process or predictive maintenance predictive maintenance process to be successful, it is necessary to nurture it with data. The equipment and machines that make up a Smart Factory are equipped with a countless number of industrial sensors that constantly monitor their operation.
The monitoring of industrial assets provides relevant data such as the temperature at which industrial machinery is working , energy consumption or the loss of operating efficiency of a machine. All this data is transmitted in real time to a data management platform that stores and processes the information.
Data analysis
From this moment on, and with the use of algorithms, a real-time data analysis is performed to identify patterns and anomalies that may occur in industrial machinery, many of which would go unnoticed by a worker. These algorithms can detect subtle changes that a human operator might miss, such as an increase in the temperature of an engine.

Anomaly detection
Anomaly detection is therefore one of the main values of a predictive maintenance system. Thanks to the ability of smart factory monitoring systems to identify unusual patterns and data, managers can uncover problems that are affecting machines or equipment. In this case, the platform will send an alert to the maintenance managers to take preventive measures before a serious machine failure occurs.
Predictive models
One of the keys to the predictive analytics needed to develop predictive maintenance lies in the creation of models based on historical data and recurring patterns. For example, based on the use of big data in maintenance and advanced analytics technologies, the algorithms that make up the platform know when it is necessary to change a part on a given machine.
Thanks to this predictive diagnosis, Smart Factory operators can plan and schedule maintenance more efficiently and at the most appropriate times, avoiding unscheduled downtime. In addition, all asset maintenance interventions are controlled and managed through the platform.
Improved productivity
Incorporating a predictive maintenance system in a Smart Factory drives productivity improvement by reducing downtime, improves planning and enables production optimization. All this translates into an increase in manufacturing ratios and a greater capacity to adapt to demand and market circumstances, which has an impact on improving the factory’s profitability.
Últimos posts

aggity strengthens its commitment to sustainability as a SILVER partner of “Fundación Empresa & Clima”.

aggity participates in the IBM Ecosystem Summit 2024 with an applied case of Generative AI in the food industry

Aggity, together with the multinational Fortinet, present an exclusive event in Lima on the application of Generative AI in Corporate Cybersecurity.

aggity participates in Smart Ports: Piers of the Future

aggity Supports the Contigo Foundation at its Annual Dinner

Challenges and Opportunities of Generative AI in Industry: Our Experience at BNEW

Official Liferay Partner in Spain
