The smart factory and its supply chain issues
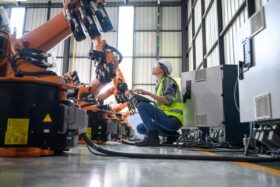
The evolution towards the smart factory is a priority for industrial organizations. However, not managing the transformation correctly can lead to supply chain difficulties.
Tabla de contenidos
ToggleIn many instances, smart factory development initiatives are disconnected from the rest of the supply chain.
The smart factory is the most important evolution that the industrial sector has undergone by improving the efficiency of production processes. This is one of the essential elements that make up the so-called Industry 4.0 and that benefits from advanced technologies such as the use of the Artificial Intelligence, the Internet of Things (IoT), the use of robots or data analytics to automate and optimize certain processes. The smart factory in Industry 4.0 brings countless benefits to organizations, but it also presents significant challenges, particularly in terms of supply chain management.
Supply chain challenges
Walking the path that leads to the factory of the future for Industry 4.0 is not a simple task because, if the transformation is not carried out in the right way, it can increase the problems of logistics and supply chain. Often, organizations make a number of mistakes in the transition to a cloud-based environment. smart factory.
One of the main failures has to do with the tendency to confuse factory optimization with business model transformation. The implementation of advanced technologies such as, for example, 5G technology, improves a factory’s efficiency and productivity, as well as supply chain management, but the evolution to the smart factory involves deeper changes in the way the organization operates.

The adoption of smart technologies does not guarantee that the business model will be transformed imminently. For the development of the smart factory to work, it is necessary to plan a strategy that considers aspects such as the advantages of implementing a certain process, the effect it will have on employees, whether there will be a return on the investment, etc. In addition, initiatives for the development of the smart factory of the future are often development of the smart factory of the future are disconnected from the rest of the supply chain. are disconnected from the rest of the supply chain, so the benefits it may provide in one section of the factory will become costly constraints in other parts of the business.
In order to avoid this common mistake in the development of a smart factory for Industry 4.0. it is essential to have a partner such as aggityThe company has a team of experts that can help with the design of an appropriate strategy for the factory and that incorporates complete solutions such as Smart Factory by aggity, which satisfactorily cover all the needs of any factory.
Managing change
Another common mistake in the evolution towards the smart factory is to underestimate the changes that will occur in the processes or the difficulty of implementing new integrations. This can result in increased costs as well as increased implementation time. It must be taken into account that a smart factory has to be a resilient and sustainable infrastructure and, to this end, it has to operate with multiple communication protocols and heterogeneous technologies, which should not create and, for this, it has to operate with multiple communication protocols and heterogeneous technologies, which should not generate incompatibilities and delays in the supply chain. Therefore, alignment between senior leadership and the use of continuous improvement teams is desirable to ensure that initiatives are properly sequenced.

Align IT/OT and governance
The goal of any smart factory is to make the supply chain more agile and efficient, also from a cost point of view, where the energy bill is a major issue. However, as more technologies and automated processes are introduced into the factory, the supply chain becomes more complex. Smart factory governance focuses not only on plant-business connections, but also on how IT, operational technology (OT) and engineering technology (IT) are managed.
For that reason, it is essential that those responsible for managing the supply chain incorporate alternative organizational models for IT/OT alignment and evolve towards organizational and governance structures in line with the new production models.
Últimos posts

aggity strengthens its commitment to sustainability as a SILVER partner of “Fundación Empresa & Clima”.

aggity participates in the IBM Ecosystem Summit 2024 with an applied case of Generative AI in the food industry

Aggity, together with the multinational Fortinet, present an exclusive event in Lima on the application of Generative AI in Corporate Cybersecurity.

aggity participates in Smart Ports: Piers of the Future

aggity Supports the Contigo Foundation at its Annual Dinner

Challenges and Opportunities of Generative AI in Industry: Our Experience at BNEW

Official Liferay Partner in Spain
